AINavi Empowers Connector Manufacturers: Boosting Equipment Autonomy and Inspection Efficiency
Connector foundries pursue product quality with more stringent standards
Connectors are one of the most important parts of smartphones.As we all know, cell phone batteries have limited capacity and need to be charged to maintain normal operation.As a charging medium, the quality of the connector will affect the charging speed, battery life, heat and safety of the phone, which are all important aspects of the consumer experience.Therefore, connector foundries pay more attention to the overall quality of the connector and join hands with brands to win consumers' favor.
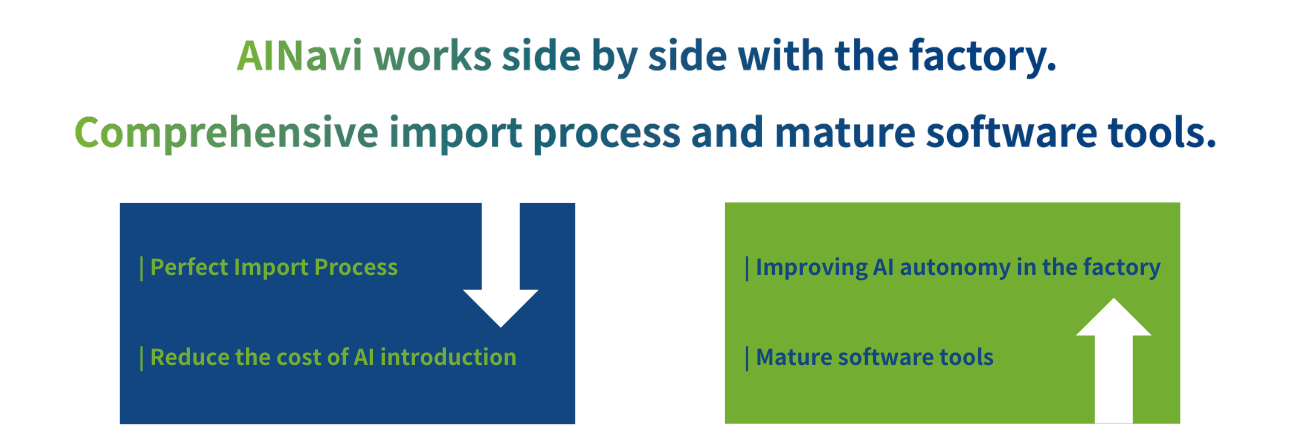
Three major problems of manual visual inspection of cosmetic defects
The quality control of connectors has many hurdles, from dimensional testing, waterproofing, plug and unplug testing to cosmetic defects.While the front-end inspections have been automated, but many manufacturers still maintain manual visual inspection for cosmetic defects.
But there are actually three problems behind manual visual inspection :
●Unstable inspection quality :
●Cost Issues :
Manual visual inspection at the end of the production line is the key to controlling production costs, and if it can be reduced, the costs can be effectively controlled.
●High risk of labor shortage :
After discovering the above pain points, a connector manufacturer, which is now an internationally renowned consumer electronics brand. They decided to introduce AI to inspect the appearance of product defects, replacing the existing manual visual inspection process, which not only reduces operation manpower, but also improves the quality of the products. In addition to reducing manpower and minimizing the impact of labor shortages on production progress, it can also improve the quality of its products and establish a deeper relationship of trust with end customers.
AINavi combines Advantech's AI mainframe to integrate existing AOI machines and promote automation of defect detection
The connector manufacturer decided to integrate AINavi into its existing AOI machine for fully automated inspection of headset contact plugs, Type C charging ports, and Type C transmission cables after evaluating the situation from various perspectives.
Due to the high demand from end-customers of cell phone brands, connector manufacturers attach great importance to the production cycle time and inspection speed.The defect identification process of each product is required to be completed within 1-1.6 seconds, and the stability and performance of the AI server are very important. Therefore, the cooperation between Spingence's AINavi and Advantech's hardware equipment can not only satisfy the customer's performance requirements, but also avoid unnecessary hardware investment to achieve the best operational efficiency.
Two major benefits of AINavi defect detection software : cost reduction and establishment of equipment autonomy
After the introduction of AINavi, the biggest benefit is that it can achieve a leakage rate of less than 1% and a machine yield rate of more than 95%, eliminating the need for the original visual inspector's manpower, which lowers the production cost and prevents the possible impact of manpower shortage.
In the future, if we want to automate the inspection of the appearance of defects in other product lines, we don't have to be limited by the AOI equipment supplier specified by the cell phone brand customer. AI can also be utilized to achieve the purpose of automated inspection, holding the ability of equipment autonomy.
However, whether the manufacturing industry can achieve the expected results after the introduction of AI applications and the level of effectiveness does not depend entirely on the underlying algorithms, but more importantly, the integration of AI and existing production line processes, and whether the field staff can be equipped with the ability of AI autonomy, which is the key to maximizing the effectiveness of the introduction of AI.