Multi-camera High-speed AI Inspection Solution
Multi-camera High-speed AI Inspection Solution
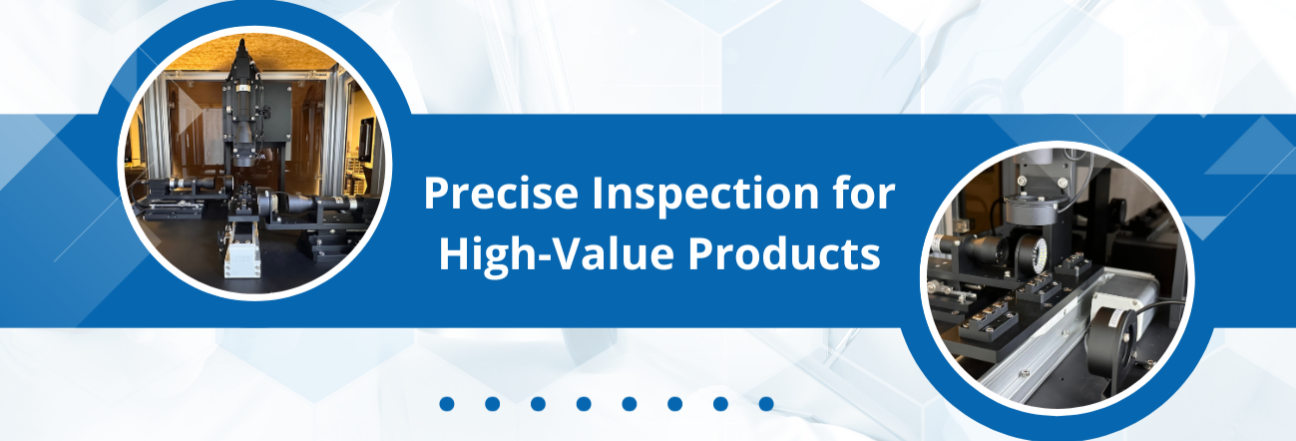
-
Multi-camera Inspection
Guaranteeing flawless products through comprehensive multi-cam inspection.
-
High-speed Inspection
Efficient inspection speed, supporting daily production capacities of up tp 400k units. -
Inspection across diverse materials
Advanced AI Models for defect detection on a wide range of material surfaces.
Detect Earlier, Save More!
Spingence provides customers with a full range of AI defect detection solutions, extending from semi-finished product inspection to finished product appearance inspection. In addition to ensuring that the products are strictly inspected, we observe that for high-value products, AI defect detection is used in the front-end manufacturing process. Early detection of defective semi-finished products and further processing will effectively help to control costs.This will effectively help to control costs and avoid the loss of production capacity due to defective products at the end of the manufacturing process or before shipment.
( Image source: Spingence )
As shown in the figure, each component undergoes multiple stages of production, and our customers set up inspection systems to optimize the yield at each station, allowing them to use it as a benchmark for production line optimization.
However, it is highly likely that defects may occur between different stations due to factors like machine operation, robotic arms, transfer devices, and dust. Thus, early rejection of defective products at different stages can prevent defective products from entering the next production phase, ultimately reducing waste.
The Necessity of Flexible AI Resource Expansion
During this process, various aspects must be considered, including dimension inspection, waterproof inspection, insertion and extraction force testing, and external defect detection. Each detail must undergo highly precise scrutiny. The presence of defects can have a severe impact on the functionality and reliability of products, potentially damaging the reputation of the end brand, a situation that manufacturers absolutely want to avoid.
Furthermore, electronic components are often produced in high volumes, making production cycle times and inspection speeds crucial for manufacturers. They aim to ensure that the defect recognition process for each unit product is completed within seconds to maintain production efficiency and meet market demand.
( Image source: Spingence )
As shown in the figure, multiple sets of CCDs are used with suitable lenses and lighting for precise multi-angle inspection, ensuring defect-free products from various angles.
To meet the demands of multi-Camera inspection and high-speed inference, Spingence offers a complete system architecture and AI engine expansion solution. Combining hardware expertise with the convenience of edge computing, it fulfills customers' performance requirements with the most suitable hardware investment for the best operational efficiency.
Multi-Camera High-Speed AI Inspection Solution
Spingence presented a comprehensive machine framework for the "Multi-Camera High-Speed AI Inspection Solution" tailored for the electronic component industry.
This precision inspection solution is designed for high-end product components or applications with specific safety requirements, such as automotive, defense, aerospace, and more.
( Image source: Spingence )
The machine features three key characteristics to meet the most urgent needs of production lines:
1. Simultaneous Multi-Camera Inspection
Using multiple sets of CCDs with different imaging devices, suitable lenses, and lighting, the machine accurately performs multi-angle inspections to ensure that products are free of defects from various perspectives.
2. Adaptable Models for Different Materials
Electronic component products often feature different materials, such as plastic and metal, on the same surface, and each material can produce specific defects.
3. High-Speed Inspection
By utilizing real-time inference with edge computing and a multi-inspection tray design, the system achieves high-speed inspection to meet the production capacity of different workstations.
To ensure image clarity under the same shooting conditions, Spingence has integrated rich professional knowledge and experience. This expertise is derived from past vision integration cases, ensuring that various defects can be captured under the same imaging conditions while maintaining image clarity.
Additionally, Spingence has in-depth knowledge of model training strategies for different industries and understands the inspection requirements of production lines. These experiences allow Spingence to fine-tune AI models precisely to provide exceptional recognition and classification capabilities to handle various defects on different materials. They can quickly train models to meet the real-time application requirements and ensure efficient and reliable defect detection.